Our PROCESS
We strive to work with the best companies using the best methods for our records. Choosing quality over everything and going as far as to buy several pressings by the same plant just to verify that no matter the color, no matter how many hands are involved, the product comes out phenomenal. Anything less and we choose to keep looking.
MASTERING
Where it all begins
The very first process in making anything relating to music (post-mixing) is the mastering. We will use several different companies for certain projects, ensuring that the right music is mastered by the right person. Companies we have (and plan to use) include the following:
Third Man Mastering (Detroit, MI)
The Mastering Lab (Salina, KS)
Sterling Sound (Nashville, TN)
Bernie Grundman Mastering (Hollywood, CA)
Please note that Astrial Pressings, nor its affiliates, claim to know the following companies personally. Please also note that while we plan to work with these companies, plans might change and we may not end up using them. We just aim to use them.
cutting
What do you call a record without a groove? plastic. duh.
The grooves of a record have to be cut in a certain manner that is specific to each and every vinyl release. Need 45 minutes of music on one disc? Different cutting method. Need that same music on a 2LP? Different cutting method. Need it on a different color? actually you don’t need a different cutting method for that but you get the point. There’s two ways to cut a record. Direct to Metal Mastering (DMM) and Lacquer Cutting. Which one is better? Honestly, we believe it’s up to your personal taste. Lacquer cutting is deeper and louder but could be more susceptible to distortion or shorter side lengths. DMM cutting lets more music be on one side and can have a lower surface noise level due to the need of constant nickel baths being moot, but the grooves are thinner and they could leave some information out. Keyword in both of these comparisons are could. We prefer Lacquer cutting over anything else so you will see us say that over and over and over again. We have worked (and plan to work) with the following engineers for lacquer cutting:
Matthew Lutthons (The Mastering Lab || Salina, KS)
Bill Skibbe (Third Man Mastering || Detroit, MI)
Bernie Grundman (Bernie Grundman Mastering || Hollywood, CA)
Please note that Astrial Pressings, nor its affiliates, claim to know the following companies personally. Please also note that while we plan to work with these companies, plans might change and we may not end up using them. We just aim to use them.
PACKAGING
With Premium sound deserves premium packaging
With the vinyl hobby, I love the packaging almost as much as the sound. The opening of the jacket sets a tone for how the music will sound, play, look even feel. With the packaging, everything matters. Everything. The printing, the style, the finishing etc. With our products, we will offer one of 2 different printing styles (granted there’s only really two out there, still.) Direct-to-Board printing & tip-on printing!
Tip-On is a style of printing that was most common in the 1950s/1960s with older records. The printing method consists of printing the artwork on a sheet of paper (ish) and then adhering that sheet onto cardstock. This creates a sense of premium just from holding it. Don’t believe me? Purchase any Analogue Productions release and let me know what you think.
D2B Printing is a more common and new age style of printing record jackets. The method is almost in the name. Instead of printing onto a sheet and adhering that sheet to cardstock, the printing happens right onto the cardstock, then the corners are adhered to each other in a way that makes pockets for the goodies. This isn’t a horrible way to make a jacket and 1000% can feel premium but we just like fancy stuff. You won’t ever see us not use this method but when we can, we will do Tip-On more than anything!
Another thing about our packaging is very minimal but probably the most important part of it all. Inner sleeves. If you buy a record nowadays you will likely get one of the following: Paper or printed. Both of which, we will never use. With paper inner sleeves comes the most damage. Storing a record in a paper inner sleeve runs the risk of scratching the surface of the disc and possibly ruining the sound of the groove as well. On top of that, it introduces dust onto the record surface, sometimes getting stuck in the groove causing a loop and worst of all, static. Printed inner sleeves provide a little more ooohs and ahhhs but they don’t really do anything more for protection. Still running a risk of scratching, dust and static. We provide our records with Polyethylene Inner sleeves or poly-lined paper inner sleeves. Which are essentially the same thing but with a layer of polyethylene in between the paper and the record, drastically reducing the risk for scratching & static by almost 89%. Granted, we are talking about plastic here which is patient zero for static and accidents happen in the plant that can scratch the record. But 89% is 89%. And once we figure out the other 11% we will use it. Trust.
PRESSING
Time to put our money where our mouth is!
Ah yes, alas we have reached the most crucial part. The pressing of the records itself. This is where it all happens. Let’s start with plating. We aim to use the closest plating facilities to our lacquer cutting engineers. Lacquers are pieces of tin wrapped in what is essentially unhardened nail polish (to loosely quote Warren Defever). These are F R A G I L E! Did I say fragile? I meant FRAGILE!! The more time they spend not being plated, the more chance for deterioration in the quality of the grooves. While this doesn’t happen as often as it arrives perfectly, it still is a chance. So we try to limit this as much as possible. If we have Matthew Lutthans cut a lacquer in Salina, we will have Quality Record Pressings plate it in Salina. Then we will send it to a company to get stampers then the pressing plant afterwards. This is where all the fun stuff happens.
A pressing plant is exactly what is sounds like, a facility that presses the vinyl discs. Here they melt PVC pellets together to make a “hockey puck.” From there it is heated and cooled simultaneously and pressed in between stampers. This lets the disc spread out and take the shape of those original grooves which is then what you play on your turntable. We will use the best pressing plants only, this way we can deliver high quality colors with high quality cuts. Third Man Pressing is one you will see often as they do the absolute most. Co-Owned by Jack White, White has made some of the craziest things on plastic. Famously, the Lazaretto Ultra LP. Which features a hologram on Side A, a side that plays from the label out to the edge, has two entirely different intros to the first song on Side B (2 grooves that co-exist right next to each other and then meet up in the middle of the track to form one groove), and two grooves underneath the center labels. With one spinning at 45 rpm, one at 78 rpm and the main record spinning at 33 1/3, making it a 3-speed record. A plant co-run by someone with that level of passion for color and vinyl gimmicks is someone that I deem an honor to work with, even indirectly. Ben Blackwell is no person to graze over either. Being involved in making The World’s Fastest Record, he brings more and more passion to the table essentially egging the makers on! Even being there for the UHQR reissue of The White Stripes - Elephant Blackwell is someone who is a role model of AP. All hail the three men of third man (Hail).
Then there’s Quality Record Pressings & RTI. RTI (Record Technology, Inc.) is a plant that has been providing exceptional quality records since 1972. Being a primary plant used for Jazz reissues and several albums, RTI has been an audiophile standard for a long time. Being the primary plant for the original line of Analogue Productions issues dating all the way back to 1991 (according to Discogs). Low noise floor and amazing quality control combine together to give the single best sound. Quality Record Pressings being an even better option.
Quality Record Pressings, launched and owned by Chad Kassem is the leader (in our humble opinion) in audiophile pressings. They pride themselves in their plating specifically. They plate lacquers the same day they receive them, as an extra hand to point to my statement earlier saying that the sooner the lacquer is plated, the better. Even going as far as to listen to the mother masters and cutting out any impurities with a microscopic knife to ensure quality. You will almost never see us press colored records at QRP. Only for the fact that, we want to keep their image alive as much as possible. If on the off-chance we deliver a subpar release, we don’t want QRP’s name tied to that. We will only ever issue “Astrial-Phile” Series pressings pressed by them. Trust when we say, we know quality when we see it. We will only bring the best with each release we make and if we don’t make something that meets our standards, we scrap it.
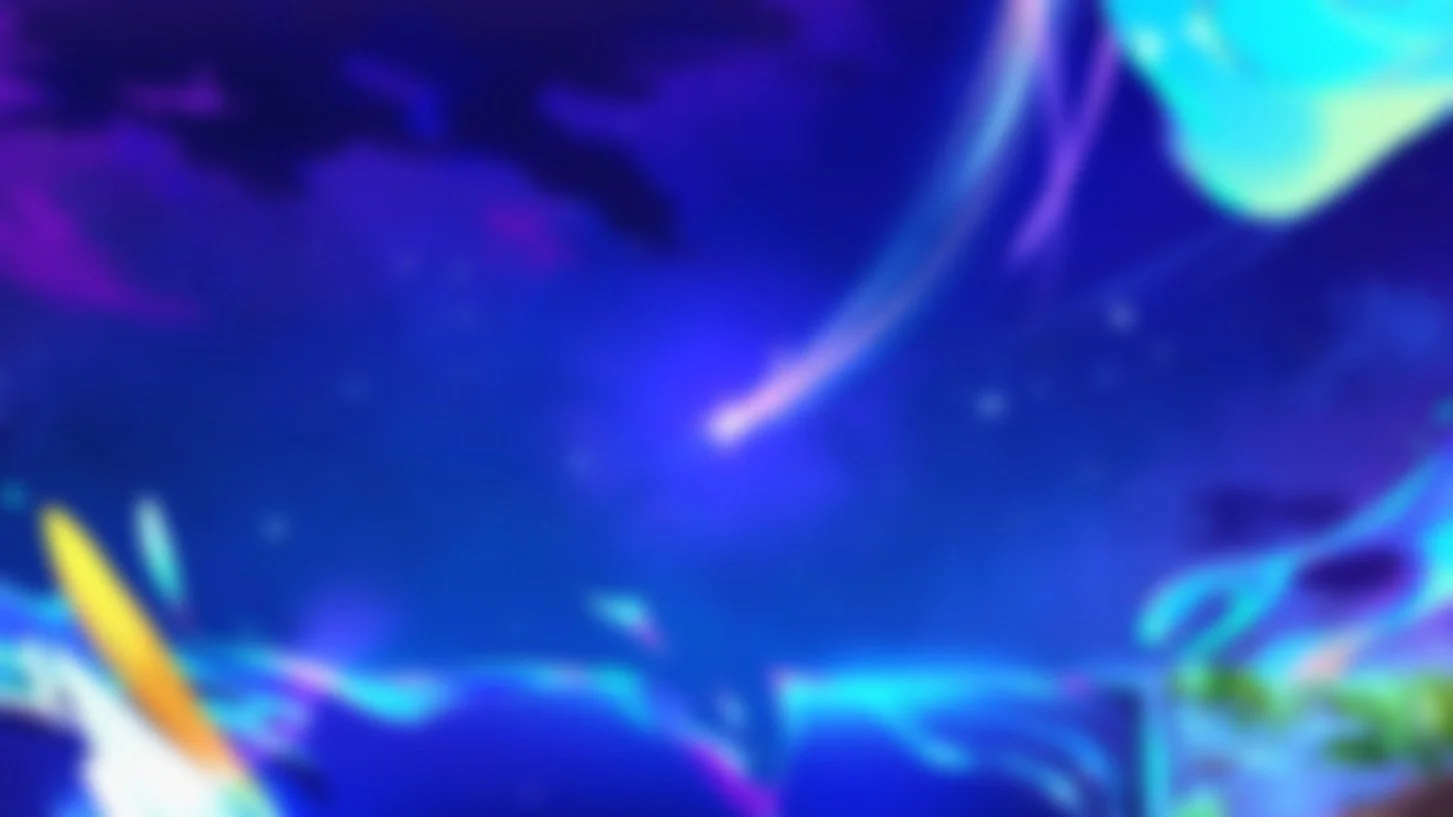